Taavi Klaos attended my lectures on Electronics and Communication Industries
(IED3100) at TTU - Tallinn University of Technology, Thomas Johann Seebeck Department of Electronics. At the end of the course he wrote a paper on Industrial Automation that I would like to introduce in the following lines.
Today we have in
industry automation three main types: PLCs(programmable logic controllers),
PACs (programmable automation controllers) and IPCs (industrial programmable
computers). Most common of them is PLC, beacuse it is oldest, cheapest and
easiest way to automate production or application. PAC and IPC are used, when
there is more complicated activity or it needs some special addition.
On last
decades difference between PLCs, PACs and IPCs have decreased because PLCs have
obtain capabilities of motion control, advanced proportional-integral-derivative
PID process control, integrated safety, features like as a web server and
networking utilities. Generally PLCs and PACs are equalizing and only IPC has a
bigger difference. At the moment PLCs and PACs are different in programming
language, which is the biggest difference. PLCs are usually using ladder logic,
but PACs are developed with more generic software tools.
Picture 1 Siemens PLC
Picture 2 Relay automation
|
Industrial automation with PLCs came in the early
1970. Before that all the logic gates were done with relays and it took a lot
of space and it was quite complicated. Relays had to maintain every year for durability
and it took time and was expensive. In Estonia I have seen until today relay
based automation. There were hundreds of relays clicking. I had to understand
why one function wasn´t done and it was really difficult without drawings. First
commercial producer was Modicon, after that came Allan Bradley and other
companies.
Communication abilities appeared in 1973 and was called Modicon´s
Modbus. This gave possibility to communicate between PCs and PLCs. Next decade
was nightmare for communications, because there wasn´t standardization and
technology was changing. At the moment some biggest manufactures of PLCs are
Siemens, Mitsubishi and Rockwell.
Every continent has his own main producers
and by this we have a lot of different communication protocols and standards. In
Europe main producer is Siemens , which gives us fieldbus Profibus. Only the
main brands are all over the world. Also it is easier to use products like
Siemens, because there is a lot of information about Siemens programming and
other help. Minus side is higher price so hardware than software. Newcomers
frequently give software for free and try to sell more hardware like this. The
first who was doing in Estonia this strategy was Unitronics and achieved good
position. Also they had really good
software suppert.
Last bigger
announcement was PAC(programmable automation controller) and it was first
defined by ARC Advisory Group in 2001. Best way to introduce PAC is something
like this: Programmable Automation Controllers that combine the functionality
of a PC and reliability of a PLC. PAC is a 2 or more processor based device
like a personal computer(PC), but orientated for industry automation. At the
beginning PACs function were doing IPCs. This were too expensive and for that
was developed controllers, what fits between PLCs and IPCs. Some producer
called they high end PLC products for PACs. End user can´t normally see
difference of them and call both of them PLC.
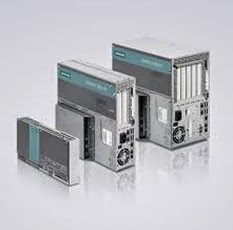
Industrial PCs (IPCs) are very resistant computers
for environment, because thay are used in mainly in hard conditins. They came a
little bit after personal computers on the 1980s. An industrial PC is PC-based computing platform for industrial
applications, processor is the same as everyday computers have. They even look
like usual competers in harded case. For touchscreen solutions there are IPCs
like screens and back of it there is processor with communication interfaces.
Robustness is achieved with heavier
metal construction as compared to the typical office non-rugged computer,
additional cooling counting with industry speciality, electronic components may
be selected for their ability withstand higher and lower operating
temperatures.
IPC could do many different applications in the same time and process
large amounts of data. Last types of IPC has same hardware as personal
computers and with this there isn´t a big hardware development costs.
Markets like
PLCs are saturated and there is a very little room for newcomers however IPCs
world is splintered by little specialized companies . They usually come from
Germany or Tawain and have a main district of applications. German suppliers
typically offers modular and open IPC hardware for specific solution every
industry then Tawainese providers started as original design manufactureres and
now also offer full-blown IPCs. In Europe in Siemens one of the biggest IPC
producers and they have good range of different IPCs. I see this is very little
market compared with PLC and for newcomers it is easier to survive.
Main thing
is to choose one application and concentrate on this.
Main advantages
of IPCs are that industries need to handle ever-growing amounts of data. This
data is often used for feedback to optimize production or to fulfil regulatory
requierements for collecting and storing data. In these days all data is
located locally, but in future this is going to cloud. This mean that good and fast internet connection in very
important, meanwhile there should be backup near to you. This will give
mirrored data and security for data lost. Most of IPCs are based on windows
operating systems, what is easy to use for all computer users.
In the last
decade we have automation everywhere in industries and without this we can´t
image a factory. PLCs are widely spread and it is very easy to use. Cheapest
ones cost below 100€ and software is free, what gives demand for all kind of
applications. Also you could expand them and add different modules. PLCs are
replacing all logic gates with realibility and flexibility. For consumer it is
easier to buy controller and use it in many ways than do something difficult
with many little things like program clock and relays.
In the future
PLCs could adopt more improvments specially from communication field. Programming
and connection should go over RJ45 socket, what is already happening. Older
ones use RS-232, RS-485, USB or something special from PLC producer.
There are
converters for RS-232 to USB and so on, but this makes sometimes problems and
you need to adjust computer for this. In some conditions it could freeze
computer or even do restart, I have feel it with mine. When we have identical
plugs and sockets on controllers we can think about communication standards.
Main hope from consumers is that producers will obtain one standard and use it.
At least not more than four five standards. At the moment we have Profibus,
Modbus, RAPIEnet and lot of other automation communication standards. After
that there is different standards for building automation too, called KNX, EIB
and so on. With this we could save much money from converting different
signals.
Converting signals also causes problems with constant data flow,
because converter could lose some data. At he moment we have a lot different
programming cables and standards and this is very costly and gives headaches.
Even one produces will change the cable standard after some years and by that
programmers should have a lot of them. Better programmers have a little
suitcase for different cables, what they use communication with controllers.
For programmers are computer manufactures even doing special computers with
different interfaces. Good example is Siemens, who is selling ready to use.
Robust programming device in notebook look for automation engineers.
Programming languages
like in ladder logic and functionblock could be the same for next decade, because
this is easy to use for everyone. PLCs should be the easiest way to automate
machines and programming language is the main thing in this. For PACs and IPCs
there are more difficult languages such as C or C++ and an off-the-shelf
package such as TwinCAT and Wonder Ware. I can´t see for PLCs, PACs or IPCs
better solutions for programming on the next decade. Maybe the easiest programs
should come with software and could be adjusted
for specific work. This is commen
in building automation controllers, but in industrial PLCs I haven´t
seen it.
Second bigger
thing is hardware. At the moment we could see on the market first PLCs and PACs
based on mobile phone or tablet hardware, what is widely spread and give better
prices. These solutions uses mainly same parts of your mobile phone and will be
easy to handle. Also they are more efficien than usual PLCs. This will give for
the hardware really good price and open software like android. It is realy good
to use touchscreen, because we have allready tablets 10 inches even bigger. In
Estonia we can see first company, who is producing these controllers with based
android software. They are advertising this with these sentences. Android based
PLC has minimum 24 input and output and it could be larger. It could me
programmed in many languages. Price is low and could used in very different
applications like traffic light-, street light-, pumping station-, smart
building managing. In the future we should see on the consumer electronics
market with open eyes and used them on other applications.
I see more
adoptions from widely spread consumer technology. One region is gaming consoles
and additions of this. Latest technology of gaming consoles what is used more
and more is 3D camera, what is used in game consoles. It game first with
Nintendo Wii and has it Microsoft Xbox and others too. Companies are selling
this solutions in ten millions and price is going down. I see 3D future in
automation industry as monitoring and managing. Operator could see and change
different views by waving his hands. Operator does not need with this a lot of
buttons on the board or touch screen, which is bigger than him. All the
necessary information is displayed on the air or on the wall and camers could
see where operator is pointing. It seems like from movie about future, but it
is next bigger thing of industury automation supervisory and managing.. Only
for the industry it is very expensive too develop new hardware or future
solutions, but adoption from other regions is cheaper as development costs are
lower.
Speaking more
about communication and data flow we can´t forget Wi-Fi. Very interesting is to
see how will spread Wi-Fi in industry automation. It could be one part of
controllers and sensors communication way. It is not possible to get good
connection from far-away places or through many walls, but factories are
usually with big open rooms and there
signal will spread good. In everyday life we have almost in every building
Wi-Fi and why not to use this for communcation in factories. It could not used
in very fast processing where speed is very important, but in usual data
transfer is possible. Fiber-optic cables goes to main routers, what should have
802.11ac standard which gives speed up to 1300Mbit/s total. We can´t use usual
Cat5 or Cat6 cables, because these maximum speed is lower.
In the future Wi-Fi
speed could be even faster. Scientist are done it, but it is not eady for
commercial use. With this there isn´t a problem of speed or amount of data. For
controllers this mean that we need to add Wi-Fi receiver from hardware and do
software changes. With signal sensors it is much more complicated, because
these should be compact as possible. One possibility is to collect for example
4 sensors output and have there a reciever and transmitter. Solutions like that
will but a lot of signals in the air. Advantage is less work for cable installers
and simpler structure. Is these signals affecting humans I don´t know. In
everyday life we live apartments and
there are sometimes about twenty different transmitters and recievers.
It is common
that controller main unit have few inputs and outputs(I/O) attached. Usually
these are digital I/O and for analog there you need to buy addition module or
when ever you want to expand you controller. Additional signal modules normally
divides for two: analog and digital signal additions. For the future I see that
controllers have only digital I/Os. Analog signals for example 0-10V are very
sensitive for noise what comes from power cables. It could make troubles for
reading measurement and make cable mounting price higer. You need to but cables
futher away from AC power cables, have a really good shield isolation, voltage signal
cables can´t be longer than 20m(not accurate with longer cable) and even then the noise could have a effect.
There is a great possibilty with voltage sensors that power cables does
inductive voltage inside it.
Voltage sensors are used mainly in building
automation or low cost solutions. In industries are mainly used 4-20mA signal
sensors. This does not admit so much disturbance and could used over 200m long
cables, but still we have not cleared noise or some affectence. For that I see
in the future that sensors are giving out digital signals. This mean that
sensors costs more and have more electronics like analog digital converter. Also
it means that we have a one common standard for sensors communication. With
this we can see more accurate measures, cheaper and easier controllers. Other
solutions is to have little data collecting points, where are analog signals
collected and converter to digital signals and sent to controller. Solutions
like this is already used and it is working.
Picture 4
Industrial robots Comau
|
In the next years the biggest profit making market
in industries for installers is industrial robot and their maintenance. This
market came on the eighties and is used in very big factories. In the world
there is few producers of industrial robots and products are expensive. In the
Europe we know some bigger manufactures like KUKA, ABB and Comau. Largest
markets for robots are in Europe Germany and Italy. Only country whos market in
industrial robots is every last year rising is Czech.
Adjusting industrial
robot to work is difficult and needs experience. It is not compared with PLCs
programming or something similar. Industrial robots have a working body and
hardware near to body. Industrial robots remind us industrial programmable
computer with body attached with it. Programming industrial robot could be done
with two ways. One option is to programm it by computer, but you need to know
very accurate dimensions of movements. The second way and more common is done
this by pendant. With this you could move robot diferents parts of it and save
moves, points and adjust the speed.
Usually installer chooses points of movement way with pendant and after that
finish programm in computer. Computer interface is better to choose different
speed and approaching angles.
People who has a
knowledge could restore old industrial robots, because these have a good value
even after restore. Bigger companies often buy new robots rather than will do a
big service. Car factories buy hundreds of robots at once an will change them
with same way. After that could used robots restore in smaller companies and
used again. It is very usefull for smaller and not so rich companies. In
Estonia industrial robots aren´t very common, but we have jobs what could be
replaced with robots. With this we can get rid of easy jobs and be more
innovative. Also with robots we need more intelligent people and pay higher salaries to give service for
robots.
Supervisory
system are spreading more and more in industries. It gives overview of factory
and helps to see barriers on factory line or some other errors. Main option of
supervisory is data and error management. It is very important to get error
messages on the same moment as this occurs. Usually this is done by
notifications from gsm, email or alert on computer screen. When we have a
notification we could resolve it and everything would work again. Other
important thing is data and command management. Operator should see everything,
what is happening in the plant. He is like a captain in the ship. Important is
even add utilities attached to system like electricity and water. Better is to
have utility measurements from many places of factory area.
With this we could
see how much different parts are spending electrity and water and do a good
survy of costs. With good supervisory system operator could avoid stops and
brakes. Other thing is that this needs to train workers who can see even a
little difference and how to react with different occasions.
One possibility how to make industrial automation installer
life easier is in the future use smart glasses. At the moment this is only in
developing position for public consumer, but when it goes popular we can see it on other applications too. This
could give us handsfree picture from different sections in factory and online
reports. One option is phone or tablet, but this is usually in you pocket or
shoulder bag and you could not notice. In bigger factories it could help
operator to solve problems. Smart glasses should have factory plan and when
problem notice comes, it directs you to right place.
Industrial
automation is basically not too complicated. It goes complex with size of
application and supervisory. Doing a program with PLCs with gsm feedback is
basic, but when you add visualization or different communicatoin ways it needs
more time. Today we can´t have a industry without automation. From that we can
see industrial automation is growing market and it needs already to renew ten
or twenty years oled programs. Second thing is that we need to solve with
automation continuosly more difficult application. This gives to our factories
more robots and sequence programs. In Estonia industrial automation came on tha
late nineties. This mean for Estonian industrial automation installers more job
from old arrangements.